The Role of Throughput Accounting in Making Decision in Small Batch Production Environment
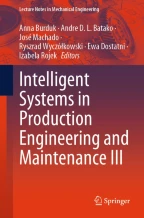
There are many challenges facing organizations. A complex and dynamic environment requires constant change and improvement of activities and reconfiguration of processes carried out in organizations. Market requirements and customer expectations force companies to seek for and apply ever new techniques and solutions. The aim of this article is to present the concept of Throughput Accounting in a production system operating under small batch production conditions as a support for decision-making. This paper also compares the results of using three different costing systems in a resource-constrained manufacturing environment. In contrast to traditional methods that focus on cost reduction, Throughput Accounting is a profit-focused method of achieving goals, based on maximizing throughput.
This is a preview of subscription content, log in via an institution to check access.
Access this chapter
Subscribe and save
Springer+ Basic
€32.70 /Month
- Get 10 units per month
- Download Article/Chapter or eBook
- 1 Unit = 1 Article or 1 Chapter
- Cancel anytime
Buy Now
Price includes VAT (France)
eBook EUR 149.79 Price includes VAT (France)
Softcover Book EUR 189.89 Price includes VAT (France)
Tax calculation will be finalised at checkout
Purchases are for personal use only
Similar content being viewed by others
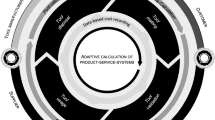
Calculation of product service systems in single and small batch production
Article Open access 02 March 2024
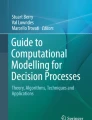
Appendix C: What to Simulate to Evaluate Production Planning and Control Methods in Small Manufacturing Firm’s
Chapter © 2017
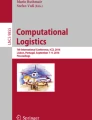
Improving Production Logistics Through Materials Flow Control and Lot Splitting
Chapter © 2016
References
- Więcek, D., Więcek, D.: The influence of the methods of determining cost drivers values on the accuracy of costs estimation of the designed machine elements. In: Wilimowska, Z., Borzemski, L., Świątek, J. (eds) Information Systems Architecture and Technology: Proceedings of 38th International Conference on Information Systems Architecture and Technology – ISAT 2017. AISC, vol. 657. Springer, Cham (2018). https://doi.org/10.1007/978-3-319-67223-6_8
- Dražić Lutilsky, I., Liović, D., Marković, M.: Throughput accounting: Profit-focused cost accounting method. Interdiscipl. Manage. Res. Xiv, 1382–1395 (2018) Google Scholar
- Goldratt, E.M.: What is This Thing Called the Theory of Constraints? North River Press, Croton-on-Hudson (1990) Google Scholar
- Pozo, H.: The theory of constraints: A case study as a strategic tooling in production management of asmall sized company. Espacios 32(2), 15–17 (2011) Google Scholar
- CIMA: Theory of constraints and throughput accounting. Topic gateway series, vol. 23 (2005) Google Scholar
- Gaspar, M., Cristovão, L., Tenera, A.: Technological innovation for industry and service systems. In: 10th Doctoral Conference on Computing, Electrical and Industrial Systems (DoCEIS), Costa de Caparica, Portugal, pp. 125–142 (2019) Google Scholar
- Gupta, M.C., Boyd, L.H.: Theory of constraints: a theory for operations management. Int. J. Oper. Prod. Manag. 28(10), 997 (2008) ArticleGoogle Scholar
- Migon, L.B., Borges, M.R.S., Campos, M.L.M.: A method for identification and representation of business process deviations. In: CRIWG 2010: Proceedings of the 16th International Conference on Collaboration and Technology, pp. 49–64 (2010) Google Scholar
- Kim, S., Mabin, V.J., Davies, J.: The theory of constraints thinking processes: retrospect and prospect. Int. J. Oper. Prod. Manag. 28(2), 155–184 (2008) ArticleGoogle Scholar
- Mehta, M.: Comparative study between traditional way and modern way of accounting. Int. J. Creat. Res. Thoughts 8(6) (2020) Google Scholar
- Sheu, C., Chen, M.H., Kovar, S.: Integrating ABC and TOC for better manufacturing decision making. Integr. Manuf. Syst. 14(5), 433–441 (2003) ArticleGoogle Scholar
- Ojra, J., Opute, A.P., Alsolmi, M.M.: Strategic management accounting and performance implications: a literature review and research agenda. Futur. Bus. J. 7, 64 (2021) ArticleGoogle Scholar
- Watson, K.J., Blackstone, J.H., Gardiner, S.C.: The evolution of a management philosophy: the theory of constraints. J. Oper. Manag. 25(2), 387–402 (2007) ArticleGoogle Scholar
- Emehelu, P.U., Falope, F.J., Agbo, E.: Throughput Accounting impact on performance, evaluation – an applied study at integrated coach factory. J. Contemp. Issues Account. 3(1), 35–46 (2022) Google Scholar
- Azzone, G., Bertelè, U., Arnaboldi, M., Chiaroni, D.: L'impresa: Sistemi di governo, valutazione e controllo. Rizzoli Etas 5th ed. (2011) Google Scholar
- Lockamy, A.: A constraint-based framework for strategic cost management. Ind. Manag. Data Syst. 103(8), 591–599 (2003) ArticleGoogle Scholar
- Bragg, S.M.: Throughput Accounting: A Guide to Constraint Management. Wiley (2007) Google Scholar
- Mabin, V.J., Balderstone, S.J.: The performance of the theory of constraints methodology: analysis and discussion of successful TOC applications. Int. J. Oper. Prod. Manag. 23(6), 568–595 (2003) ArticleGoogle Scholar
- Wojakowski, P.: Production economics with the use of theory of constraints. Res. Logist. Product. 6(1), 79–88 (2016) ArticleGoogle Scholar
- Perisa, A., Kurnoga, N., Sopta, M.: Multivariate analysis of profitability indicators for selected companies of croatian market. UTMS J. Econ. 8(3), 231–242 (2017) Google Scholar
- Nakajima, M., Tobita, K.: Reconstruction of the management accounting system based on Material Flow Cost Accounting (MFCA) and Throughput Accounting (TA): expansion of the concept of opportunity cost. Kansai Univ. Rev. Bus. Comm. 18, 35–49 (2019) Google Scholar
- Islam, K.A.: Throughput accounting: a case study. Int. J. Finan. Bank. Res. 1(2), 19–23 (2015) Google Scholar
- Şimşit, Z.T., Günay, N.S., Vayvay, Ö.: Theory of constraints: a literature review. Procedia. Soc. Behav. Sci. 150, 930–936 (2014) ArticleGoogle Scholar
- Plinta, D., Radwan, K.: Improving material flow in a modified production system. Appl. Comput. Sci. 19(1), 95–106 (2023) ArticleGoogle Scholar
- Więcek, D., Więcek, D., Kuric, I.: Cost estimation methods of machine elements at the design stage in unit and small lot production conditions. Manage. Syst. Product. Eng. 27(1), 12–17 (2019) Google Scholar
- Klimczak, K., Mleczko, J., Więcek, D., Działalność gospodarcza przedsiębiorstw w warunkach Przemysłu 4.0. Polskie Wydawnictwa Ekonomiczne, Warszawa (2023) Google Scholar
Author information
Authors and Affiliations
- Faculty of Mechanical Engineering and Computer Science, Department of Production Engineering, University of Bielsko-Biala, Bielsko-Biala, Poland Dorota Więcek, Dariusz Plinta & Katarzyna Radwan
- Dorota Więcek